Industry unites over biosecurity
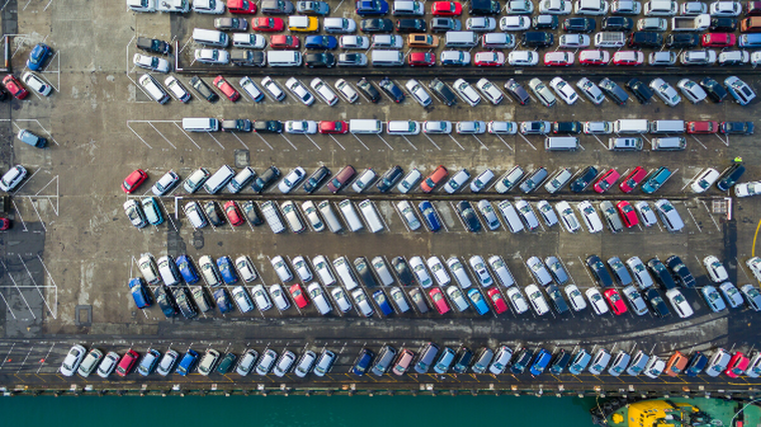
Industry associations representing the used and new car sectors are working together to find about $70,000 a year to keep a vehicle heat-treatment facility operating at Ports of Auckland (POAL).
David Vinsen, chief executive of the Imported Motor Vehicle Industry Association (VIA), says the facility is seldom used but it plays a critical role in keeping the supply chain moving if a biosecurity threat is found on an imported vehicle at the wharf.
He notes VIA and the Motor Industry Association (MIA) have agreed to share the costs of keeping the service in place, with them finding 45 per cent and 55 per cent of the necessary funds, respectively.
The facility is operated by BioVapor and Vinsen says the company approached the new and used vehicle sectors for financial support after POAL increased the annual ground rent.
Vinsen adds: “We got together with the operator, the ports and shipping lines and did some analysis. From that MIA agreed to pick up its share of the tab and used vehicle people will do likewise.
“We have got general agreement in the used vehicle industry towards paying the cost of the rent but are now just working out how we’re going to collect it.
“It is most likely that the logistics companies will collect it from their customers and it will work out at about 50 cents a car.”
He explains all used imports from Japan are heat treated before being shipped here, but the facility at POAL acts as a contingency in case any infestation – such as brown marmorated stink bugs – or contamination is found in a vehicle by Ministry for Primary Industries (MPI) officials on its arrival in New Zealand.
“If something was found by MPI inspectors that was considered a biosecurity threat it would mean trucking every car from that shipment off the port in covered wagons to be heat treated somewhere inland,” says Vinsen.
“Having the heat-treatment facility at the port means any affected vehicles can be treated on the spot, which speeds the whole process up.
“We want to have that insurance because we have been through some challenging times such as the stink bug crisis, the Covid-19 interruption, and MPI moving its staff back to New Zealand from Japan.
“We know when there’s disruption the whole supply chain grinds to a halt and we don’t want that to happen.”